インジェクション成形とは? メリット、デメリットをご紹介
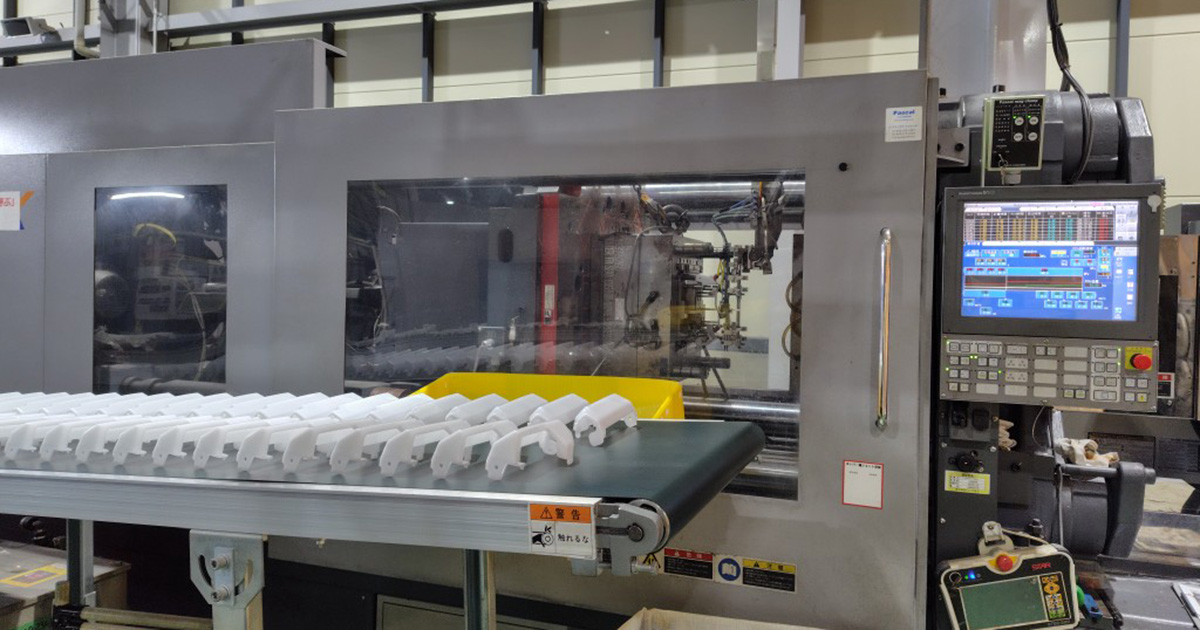
プラスチック成形の中でもっとも多く用いられる成形方法の「インジェクション成形(射出成形)」。
ここでは、インジェクション成形はどのようにして行われるのかそのあらましと、メリットやデメリットをご紹介します。
インジェクション成形(射出成形)とは
インジェクション成形は、熱可塑性や熱硬化性のプラスチック原料を使って、複雑な形状の部品を大量生産する成形法です。
インジェクション成形は、「溶かす・流す・固める」という3つの基本工程で行われます。
- 溶かす
プラスチック原料を加熱して溶融状態にします。 - 流す
溶融したプラスチックを高圧で金型に射出します。 - 固める
金型内でプラスチックを冷却し、固化させます。
プラスチック成形の中でもっとも多く用いられる成形方法であり、ほとんどのプラスチック成形品がこのインジェクション成形で作られています。
金型を使用することで、同じ形状の製品を短時間に多数生産でき、
外部要因に影響されにくいため、プラスチック製品の完成度、寸法精度がとても高く、
製品ができあがるまでのサイクルタイムも短い。
という特徴があります。
インジェクション成形は、大量安定生産に適した成形法です。
インジェクション成形機の構成

インジェクション成形機は、大きく分けて「射出ユニット」、「型締ユニット」、「コントロールユニット」の3つで構成されています。
射出ユニット
射出ユニットは、プラスチック材を溶かし、金型に高圧で流し込むのが役割りです。
内部は主に、「ホッパー」、「シリンダー」、「ノズル」によって構成されます。
ホッパーから入れられた材料はバンドヒーターによって加熱されたシリンダーで溶け、ノズルから射出されます。
型締ユニット
型締ユニットは、金型をとりつけ、金型の締めつけや開閉するのが役割です。
また、成形品の冷却も行います。
内部は、「型締シリンダー」と「金型(固定側と可動側)」によって構成されています。
金型を開閉することで材料を充填したり、成形品を取り出したりします。
金型の締め方の動作方式としては、油圧で行う「直圧式」と、電動サーボモーターで行う「トグル式」の2つがあります。
コントロールユニット

コントロールユニットはインジェクション成形機の制御部です。
射出の速度やシリンダー温度、圧力、金型の温度、樹脂の射出量などの、成形条件をコントロールします。
インジェクション成形機の種類(動力源による分類)
インジェクション成形の射出や型締に必要な駆動装置の動力源としての代表が、「電動式」と「油圧式」の2つです。
電動式
電動式は、サーボモーターを用いて、速度・圧力・位置などの動作をすべて制御します。
電動式のメリット、デメリットは以下のとおりです。
電動式のメリット
- 製品の成形精度が高い
サーボモーターにより射出装置の制御が正確にできるため - 油圧式と比較して40%~50%省エネ
必要な時に必要なだけモーターを駆動させるため - 成形サイクルの短縮
4つ以上の独立したモーターにより成形工程を並列進行させることができるため - クリーン
衛生的、油不使用、冷却水を大幅削減
電動式のデメリット
- 油圧式に比べ価格が高め
- 制御に無理がきかない
油圧式
油圧式は、油を閉じ込めて、その圧力を離れた場所に伝えることで大きな力を出します。
油圧式は、古くから利用されている方法です。
油圧式のメリット
- 電動式と比べて成形機の価格が安い
- 電動式と比べて条件設定の幅が広い
油圧ならではの操作感覚があり微調整などが可能
油圧式のデメリット
- 消費電力が大きく音も大きい
- 寸法が安定せずブレが生じるため再現性に乏しい
成形の安定性、成形サイクルタイム短縮、環境への配慮、省エネの観点から、当社は電動式の成形機を多く採用しています。
インジェクション成形の工程

インジェクション成形の工程は、次のステップに分かれます。
金型はインジェクション成形において最も重要な要素の一つです。
設計された金型が正確であることが、製品の品質に直接影響します。
金型は通常、金属(主に鋼やアルミニウム)で作られます。
プラスチック原料(ペレット状や粉末状)がホッパーから射出成形機に供給され、スクリューによって加熱され溶融します。
溶融したプラスチックがスクリューによって高圧で金型に射出されます。
このプロセスは非常に高速で行われます。
充填圧力は、スクリューの回転数やシリンダーの背圧で調整可能です。
射出後、金型内のプラスチックに一定の圧力をかけ続けます。
これにより、収縮や変形を防ぎ、製品の寸法精度を向上させます。
プラスチックが金型内で冷却され、固化します。
冷却時間は製品の大きさや厚さによって異なります。
固化した製品が金型から取り出され、次の製造サイクルが始まります。
このような流れで、複雑な形状の製品を素早く、大量に、安定して生産できることができます。
一方、複数の工程に分かれているため、各工程それぞれにインジェクション成形を成功させるためのポイントが存在します。
使用するプラスチック材の性質や充填速度・時間、金型の構造・温度・保圧時間、冷却後のプラスチックの収縮、など考慮すべき点はさまざまです。
製品の仕様やお客様のニーズ、納期などを踏まえ、最適な成形条件を設定します。
インジェクション成形に使用される樹脂


インジェクション成形に使用される代表的な材料を紹介します。
ポリプロピレン(PP) | 耐熱性と化学耐性に優れ、食品容器や自動車部品に使用 |
---|---|
ポリエチレン(PE) | 柔軟性と耐薬品性に優れ、包装材や容器に使用 |
ポリスチレン(PS) | 透明性が高く、食品パッケージや文房具に使用 |
ABS樹脂 | 耐衝撃性と成形性に優れ、電子機器や自動車部品に使用 |
ポリカーボネート(PC) | 透明性と耐衝撃性に優れ、CDやDVD、安全メガネに使用 |
ナイロン(PA) | 強度と耐熱性に優れ、機械部品や自動車部品に使用 |
ポリアセタール(POM) | 摺動性と寸法安定性に優れ、精密機械部品に使用 |
これらの材料は、製品の要求特性や用途に応じて選択されます。
また、添加剤を加えることで、強度、耐熱性、難燃性などの特性を向上させることも可能です。
インジェクション成形のメリットとデメリット
メリット
- 同一品質の製品を大量に生産するのに適しています。
- 幅広い種類のプラスチック材料が使用可能で、特定の用途や機能に応じて材料選択ができます。
- 一度金型を作れば、その後の生産コストは低く抑えられるのも利点と言えます。
- 成形後の製品はそのまま使用可能で、後工程が最小限ですみます。
デメリット
- 金型の製作費用が高いため、少量生産には不向きです。
- スプールやランナー等製品以外の部分も成形されるため、その分の材料の無駄が生じます。
- 大型製品になればなるほど、大型のインジェクション成形機と金型が必要となりコスト高となります。
まとめ
インジェクション成形は、プラスチック成形の中でもっとも多く用いられる成形方法であり、大量の製品を安定して成形できる方法であることをご紹介しました。
エレック北上は
お客様にインジェクト成形品をジャストインタイムにお届けするため、製造現場でリードタイムをどう短縮できるかはとても大切な事項です。
リードタイムの要素の一つに成形サイクルがありますが、上で述べた電動式の成形機は成形サイクルの短縮に寄与できます。
このため、当社では、電動式の成形機を多く採用しています。
電動式は、成形サイクル以外にも、環境、省エネのメリットも大きい方式です。
また、型替え・段取り替え時間短縮のために、230t以上の成形機には全てマグネットクランプを取りつけています。
お客様納期の厳守、さらなる生産性向上にこれからも取り組んでまいります。
\ エレック北上 部品加工の総合力をぜひお試しください /
電話でのお問い合わせ、リモートでのお打ち合わせもお気軽に